Equipment Inventory Management Practices for 2025

Of course, improper equipment inventory will lead to unneeded expenses, management disturbances, and growth-stifling opportunities. From an arborist to a fleet manager, it has never been more critical to keep tabs on all equipment. A business must spend some time sharpening its equipment inventory management tools in my opinion, the following reasons make sense.
First and foremost, cutting costs and improving efficiency should be the priority, with equipment tracking taking center stage. In this scenario, a loss of time searching for rigging ropes by the climbers will result in setbacks and disrupted team flow, potentially ruining the entire operation—not to mention hurting the company’s image. These challenges underline the importance of understanding how to manage equipment inventory effectively. By staying organized and proactive, businesses can ensure their teams have the right tools at the right time, avoiding operational hiccups and preserving their reputation.
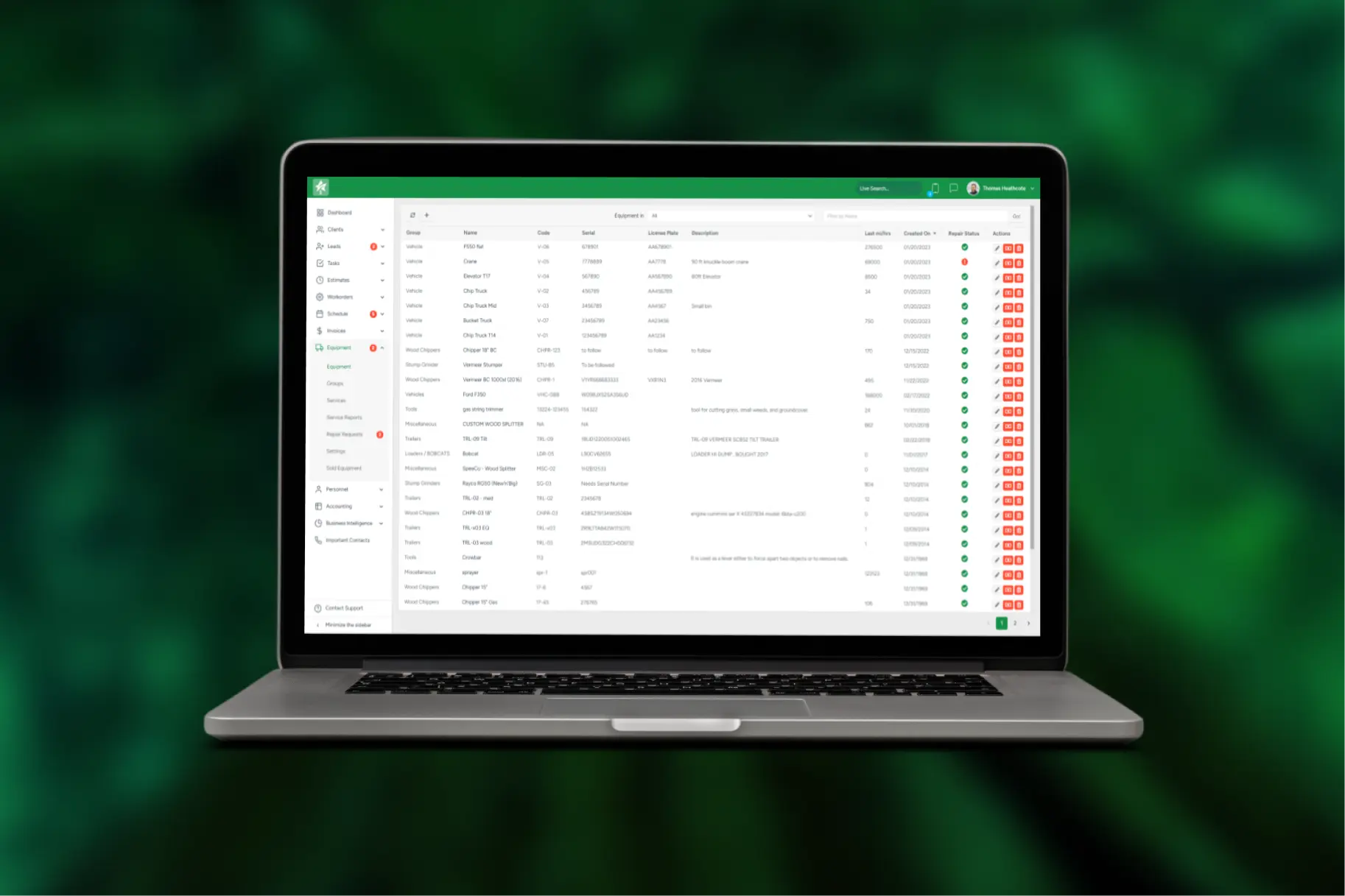
Last but not least, inventory oversight reduces oversight errors. When there are no resources available or maintenance is actually overdue, it would prevent disruptions and cost requirements if the repairs are infrequent. All the planning becomes fathomable after orienting with the resources available and their precise location along with their intended purpose; effectively enhancing operations.
But what is a game changer? As we head into 2025 there is a shift in the trend as the most adopted instruments and equipment have changed. The game has changed with the introduction of ArboStar Applications, satellite tracking systems, and many others. Businesses are heavily relying on these tools in order to enhance processes, ensure occupational compliance, and lessen the excuses whereby one person is left saying "I thought you had it!"
In the final analysis, the most advanced technologies in the markets such as arborists, construction, medicine, as well as other industrial areas are reliant on robust stock systems. You can’t afford to be instinctive knowing that lives, trees, or even costs are reliant on the machinery that is available in your tools. Come start looking for smarter methods for dealing with tool stock as in the end you might need them to be successful.
What is Equipment Inventory Management?
Equipment management can be defined as the control or tracking of all the inventory equipment, tools, machines, or resources that every business needs, and this process can be called inventory control. Primarily, it has only two significant goals which are to maintain, arrange, and boost productivity by managing equipment inventories as well as making certain that no money is wasted and costs are kept down. Exaggerating one aspect of this is safe: It’s not that easy. Equipment, in contrast to fixed assets, flies about. It travels from one job site to another, from one storage facility to another, as well as various teams and projects. It is this that makes it intricate.
Let’s break it down into its core components:
-
Inventory Management: Picture operating a tree-care enterprise without being able to locate your stump grinder. Sad! He who possesses a laser-focused efficient effective inventory management system clearly understands the fact that sunscreen is not all about lotion. Where exactly are your devices and resources? It also allows for managing logistics optimization. Getting correct equipment when needed. This can be transformed using GPS or QR codes and inventory.
-
Performing Maintenance: Any equipment that is not well cared for can potentially cause distress. Whether it is during regular customization, such as ensuring chainsaws are efficiently cutting sharp edges, baking pizza or excavator dozers are sights to behold. Force that has been prepped for action, scheduling inspections allows maintenance to be performed before emergency repair measures have to be taken.
-
Inventory In Supply Chain Management (SCM) Precost Analysis Chris Castiglie: The lifespan of any resource or device is irreplaceable since it is the operating age of the device. Resource management tracking efficiently records when the device begins to wear out even if its usage is almost none and aids in determining when to replace when it wears out. This saves individuals from looking for replacements when it’s too late.
To tell you how crucial inventory management is, first consider arborist services with climbing ropes, rigging kits, and bucket trucks; without any measures monitoring on that equipment, slack will become intolerable. Also in construction work, lack of awareness of available working implements, such as mixer or holder, will not only lead to a backlog of progress of work but also business in general.
As a result, businesses can save time and money and increase operational efficiency. This can be accomplished by the use of modern systems such as inventory management in 2025 and beyond.
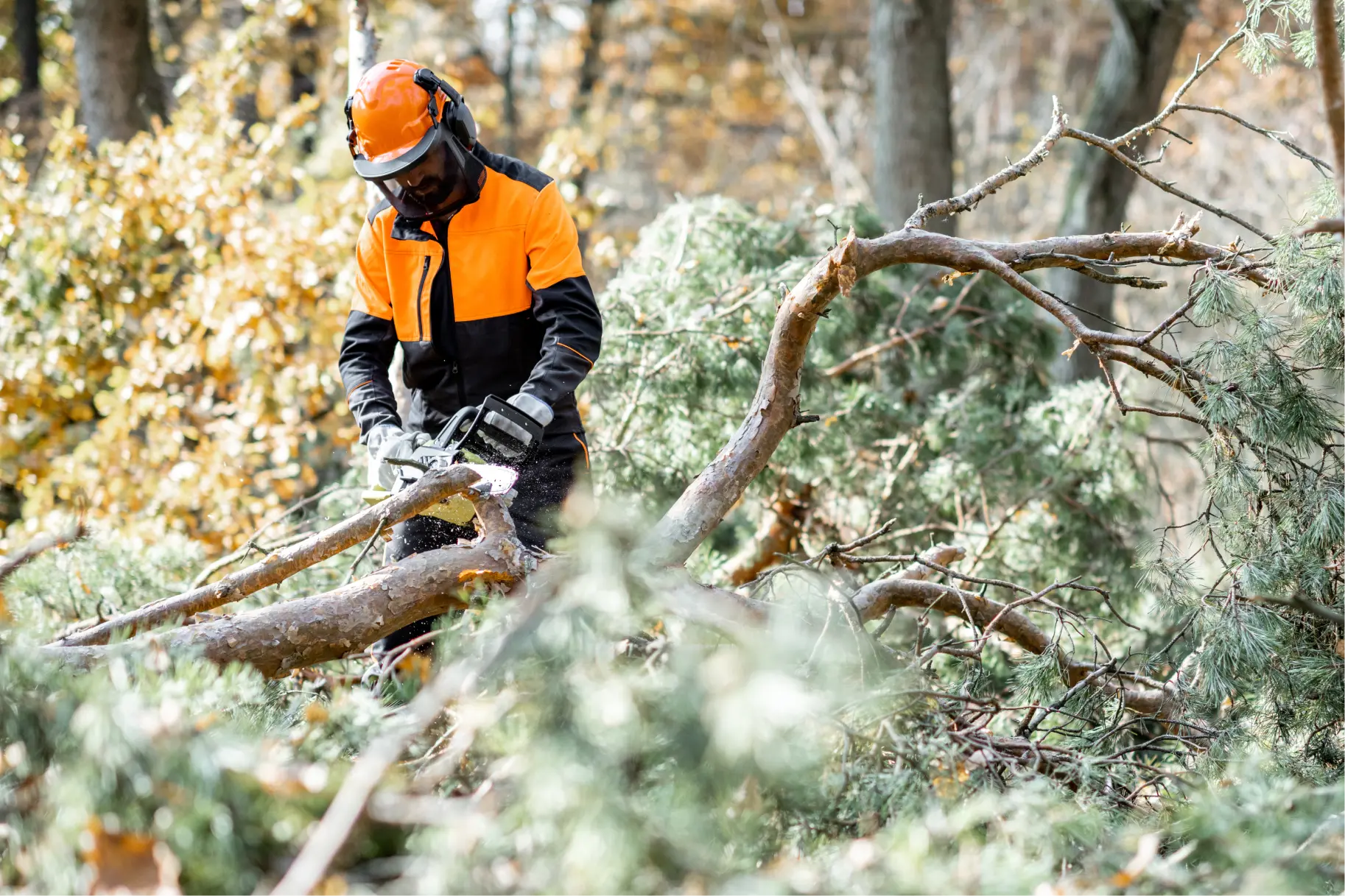
Managing Equipment Inventory
Proper management of equipment of the business operations is crucial for its smooth running and also to prevent expensive mistakes. Whether it’s a case of chainsaws and wood chippers or excavators and forklifts, some practices can help one manage the equipment properly. Here’s a step-by-step cognizance to assist you with your inventory management efforts.
1. Have Periodic Inventory Surveys
First start with an all-rounded equipment check. How many do you have, what do you have, what is the condition, and where are the items? This step ensures that no tools that are out of place or damaged are missed in its account.
2. Create Inventory Classifications
Sort and group equipment based on their type, use, and value index. For instance, daily climbing ropes should be stored away from tree stump grinders which are less frequently used. This reduces the time taken to search for the equipment and puts the more important ones at the forefront.
3. Acquire Tracking Systems
Move from keeping records of manual logs to automated ones. Using barcodes, QR codes, and even GPS will provide more information on the equipment and how it is used. These tools reduce losses and items being misplaced in the first place.
4. Repairs and Maintenance Should Be On Time
Some tools are easier to use than others and some tools are well kept and maintained. Implementing these maintenance schedules on the more important tools will help offset any unexpected problems. For example, requests for maintenance on chainsaws every month and that heavy machines are routinely checked.
5. Empower Your Staff
It's common to hear that a system to be successful must have people who are well-trained to effectively implement the processes required. ASTM has provided several standards that concern the tracking of assets. Such measures, like logging in and out of assets also increase the usefulness of the assets.
6. Conduct Periodic Appraisal and Adjustments
Your aim should be retained somewhere in sight so that the operation does not assume an independent existence. Enable periodic appraisals of established inventory management to detect shortcomings and suggest possible corrective measures. Prepare to make possible operational retrospection, such as equipment that is not fully utilized or a better arrangement of the store.
Pro tip: Tyres are about the only useful tool that need not be labeled because labeling it saves time spent hunting for it.Indeed depreciation forecasting is a proficient aim for wise replacement planning. Undoubtedly, no time would be spent on ensuring that your inventory of equipment is in perfect tilt, with these best practices in place.
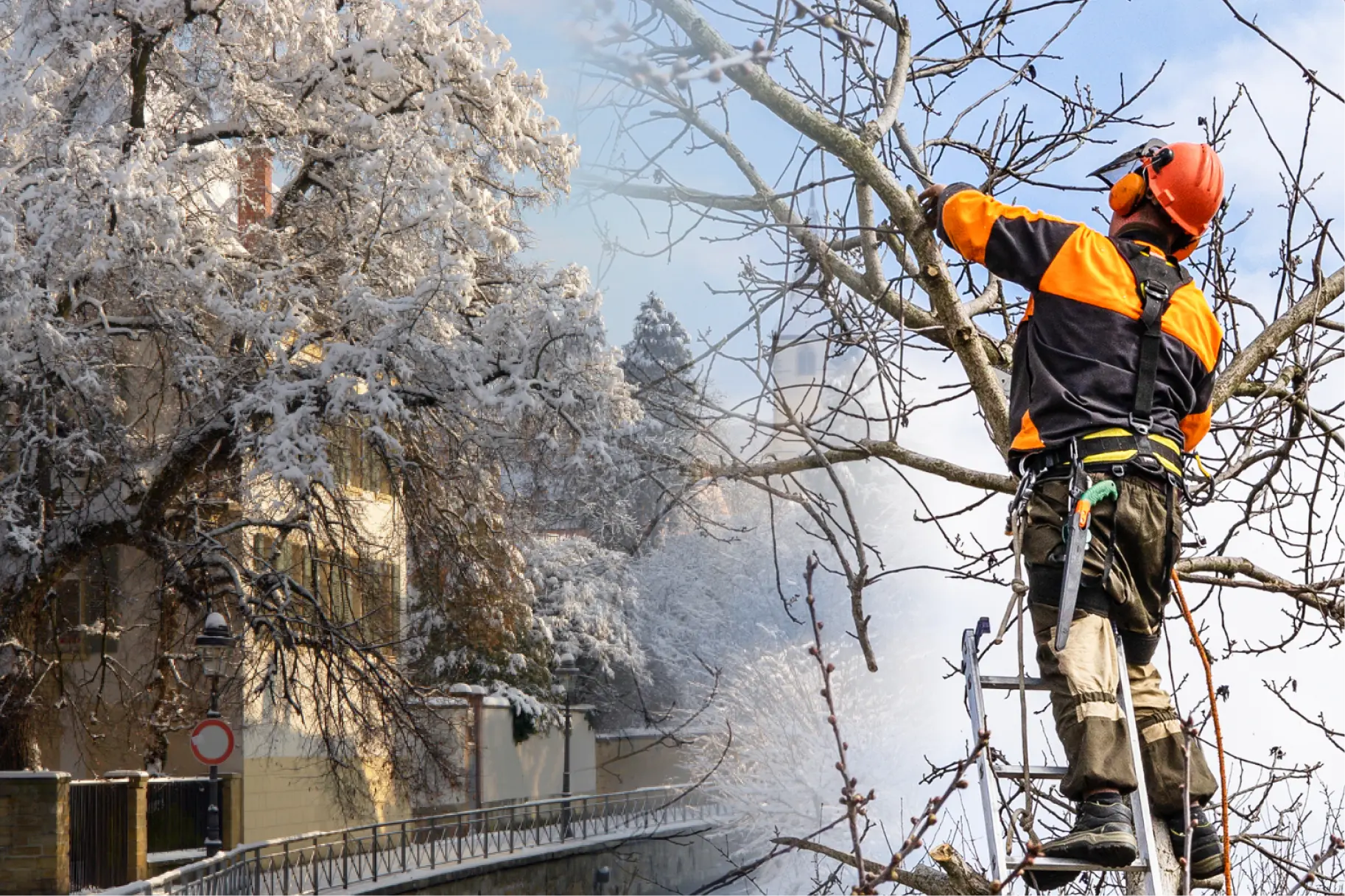
Best Inventory Management Software
The central aspect of meeting clients' requirements is effective tracking and monitoring of devices.The challenge of tracking equipment inventory with outdated manual spreadsheets is now a thing of the past; modern guidance systems ensure efficiency and precision in 2025.
What do you look for in a modern management tool? Well look out for a user interface that is not too complex for your workforce, no more guessing about where an asset is only accurate information on the location of that piece of equipment, and great reporting capabilities assist in informed decision-making. In short, the ideal management application goes beyond just tracking the equipment to integrating the rest of your business processes.
Let's take ArboStar as a case in point. It is specially designed for tree care and landscaping companies and comes with the following features:
-
GPS tracking plus live job maps allow a user to determine the exact position of his equipment in no time.
-
Scheduling, payroll, and fleet management integration changes the game by layering not only tools, but all of the crew and operations.
-
Sophisticated analytical reporting, allowing for visibility of equipment utilization, maintenance intervals, and cost efficiency measures.
So what are the advantages? First, the software eliminates human mistakes, for example, it will no longer quite be a guesswork trying to figure out where the stump grinder was last used. Also, it helps in being more efficient as the tools needed for the job are easily accessed and used. Moreover, it saves wastage of equipment as well as work inefficiencies.Picture this: you receive an alert when it has been days without using your bucket truck or when a chainsaw needs servicing.
Although the use of solutions like ArboStar makes recording assets of the equipment in the inventory much easier, do not take ArboStar lightly. There is more to it than mere ease.